Need help or have a Question?
Send us a Request
Please send us a request if you need help.
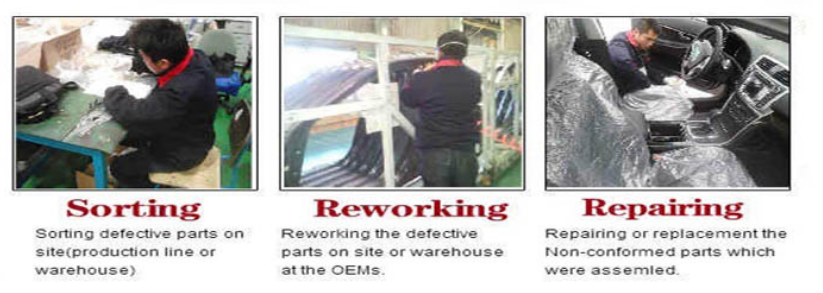
Towards our goal: Zero dectect: Zero PPM
Askawa Inspection has the ability to create photo or written work instructions and design processes from scratch if not available from our customers. We always make sure to get Work Instructions approved from our customers before starting work. Our supervisors communicate electronically with customers to share work instructions, data, pictures, etc., to prevent delays. Our inspectors are also familiar with a wide variety of automotive parts and have developed specializations after years of experience.
- Wire Harnesses Leather and Trim
- Weld Assemblies
- Castings
- Sheet Metal
- Stampings
- Rubber and Moldings
- Interiors (Plastic, Headliners, etc)
- Engine and Transmissions
- Axles, Gears, etc
Our staff of experienced inspectors at ASKAWA, service our customers 24 hours a day, 7 days a week, and 365 days a year. We can provide sorting and inspection services on all three shifts at your location, our warehouse, or travel to a customer site.
- Visual Inspections (Appearance conformity, Cosmetic defects, etc)
- Go, No-Go Gauging Inspections (Push, Ring gauges etc)
- Electrical Testing Inspections (Circuits, Wiring, Voltage checks)
- Dimensional Inspections (Caliper, Tape Measurement)
- Location Inspections (Using Jigs and Fixtures)
- Functional Testing Per Customer Specifications
- Resident Engineer / Resident Inspector
Askawa Inspection Promise
– Highly trained personnel
– Dedicated inspectors
– 100% final inspection
– Greater efficiencies in process
– Daily work report
Need help or have a Question?
Send us a Request
Please send us a request if you need help.